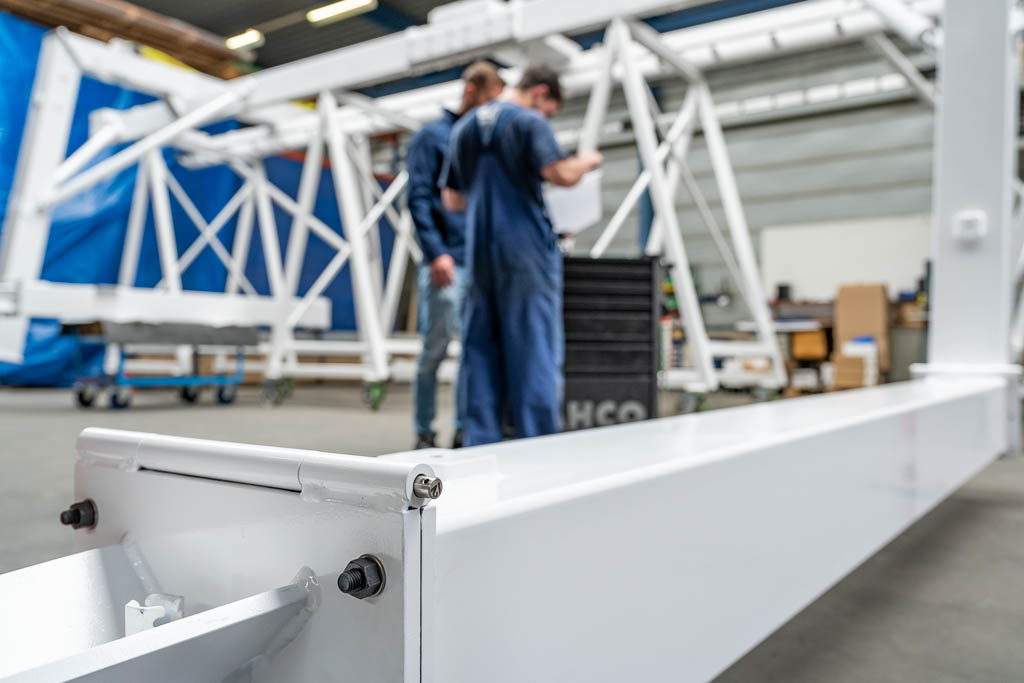
Mechanical Ground Support Equipment (MGSE) is the equipment used during Assembly, Integration and Test (AIT) of Space Equipment. Examples of MGSE are interface adapters for vibration tests and tip and tilt trolleys for assembly. Another example of MGSE are functional test frames regarding the deployment of solar array panels. A recent example we take pride in is the Deployment Rig for the solar arrays of Metop.
Regarding solar array, we take great pride in the fact to have manufactured the Vertical Integration Rig and the large red Protection Covers for the solar array of the Artemis mission.
For the Galileo Test campain at Estec we did co-engineering and manufacturing of the tooling needed for the EMC-test, the weight determination test and the termal test. Regarding EMC-testing, we take great pride in the collaboration with ETS in engineering, manufacturing and installation of the Bepicolombo test support. This project included materials like stainless steel, titanium, wood and special plastics. This project also included the refurbishment of the wooden air pallet.
Services

West End has had its own engineering department since the 1970s. The drawing office has kept up with the technological developments over the years. Our engineers provide the manufacturing department with production drawings
FEM analyses
We can also perform analyses for the components in a system that need to bear heavy loads, using the Finite Element Method (FEM). Our engineering department helps our customers with these calculations which determine (operational) reliability. We also use the FEM analyses for the final choice of materials and the details of the product geometry.
West End offers solutions for the refurbishment of old, existing systems through to the manufacture of new ‘special hardware’. Our engineering department provides indispensable support in the detailed design and system documentation.
Product documentation
During the entire manufacturing process, and often afterwards as well, our engineers remain involved in the products we make or repair. This results in detailed product documentation, where changes for the manufacture or modifications received from the customer are documented meticulously. This provides great advantages in maintenance, refurbishment or repairs in the future.
As-built drawings
West End Machinefabriek can also make ‘as-built drawings’. Changes to the product for manufacturing efficiency are updated in the CAD model and the production drawings, making it simple to duplicate in the future.
Built to spec
Using your requirements and specifications as a basis, our engineering department can develop the product design in greater detail and prepare it for manufacture. Our engineers also perform FEM calculations, to check critical construction elements and the final choice of materials. Of course the assembly drawings and detailed drawings are guaranteed for refurbishment, reconstruction and production documentation purposes.
Built to print
West End can also use the 3D models and detailed drawings supplied to switch quickly to producing parts or products. Precisely in accordance with the instructions, specifications and requirements.
High Precision, huge parts
West End also uses 3D measurement technology for the quality assurance, allowing us to provide the product documentation with 3D measurement reports. This is done using a 3D measurement arm. West End can also measure large frames and systems with our 3D optical measuring equipment.
Technology
Surface treatment
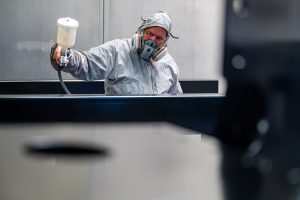
West End is proud when an airplane gets into the air for the first time thanks to our parts. We apply care and dedication to the refurbishment, manufacture and engineering of our products and can also apply this to their finishing, if desired.
We use three different blasting techniques to finish our work pieces and production, allowing us to achieve a wide range of roughness. We use ceramic powder, glass beads or corundum. These sand blasting materials are sustainable and suitable for multiple use.
Ice blasting
Besides the conventional blasting using grit, West End was one of the first companies in the Netherlands to use sustainable ice blasting, which is the use of frozen water drops. A filter system enables 100% of the waste material to be separated. The desired surface quality remains at the same high level compared with conventional blasting techniques.
Coating
West End has two paint lines. We use wet paint and we can paint electrostatically, to achieve optimum paint seal and quality.